該文主要內容引用英特爾一篇技術文章“Thermo-compression Bonding for Fine-pitch Copper-pillar Flip-chip Interconnect– Tool Features as Enablers of Unique Technology”
2010年Iphone 4橫空出世,輕薄又強大的性能深深震撼了消費者。消費電子產業注定要在輕薄的賽道上狂飆猛進,而PC領域更不會獨善其身。
很快時間來到了2年后,全球半導體領導者英特爾的芯片封裝研發總部的會議室進行著一場激烈的技術路線定型爭論,爭論的最終結果必將深刻的影響公司的下一世代的全球競爭力,數百億美元的投資以及龐大的供應鏈的去存。當前成熟的倒裝回流焊(Flip Chip Mass Reflow) 封裝工藝注定很快成為明日黃花,其已經無法應對新產品對輕薄的高要求,尤其是切入到14nm工藝后,基板(substrate)和晶片的厚度將成倍下降,熱應力下的翹曲效應使得凸點橋接(Solder Bump Bridge) 失效異常嚴重。
?
行業巨頭們都在提出自己的方案,簡而言之兩個方向,要么將晶圓的刻蝕工藝拓展到封裝,要么在兼容當前的基板封裝但研發全新的設備和工藝解決翹曲問題。每個方案都牽扯到巨額的成本問題。尤其是對于英特爾而言,PC行業的生態鏈龐大而復雜,放棄兼容性無異于傷筋動骨甚至自廢武功。
最終基板封裝方案獲得了勝利,下游廠商的兼容性得到照顧,所有的人都心潮澎湃,因為這必將是場豪賭,新一代的封裝設備將挑戰機械加工的極限。對新設備的要求無比苛刻: 能貼裝更薄的晶片,支持多晶片貼裝,更小的晶片間距離,更緊密的凸點陣列,以及3D晶片堆疊。事實上就連英特爾公司總部也為這個賭注深深捏了把汗。
工藝方向很明確:熱壓鍵合 (Thermo-compression Bonding, TCB)。這項工藝并不是新事物,早在上世紀八九十年代,摩托羅拉公司就有過應用。然而新紀元對設備的精度要求卻不可同日而語。其工藝機理如下圖:
-> BondHead(貼片頭)自帶加熱源,可以將撿起的晶片(Die)迅速加熱到臨界錫球融化溫度;
-> 在基板于晶片的凸點物理位置接觸的一瞬間, BondHead從壓力敏感控制轉為位置敏感控制,并迅速加熱到錫球融化溫度以上保持數秒,之后BondHead迅速冷卻,使得上下凸點之間的連接變為固相。焊接過程完成。
該工藝的設備關鍵工藝指標最主要有兩點:一是貼放的精度,在Z方向位置控制靈敏度要達到驚人的1微米,且與壓力控制轉換無縫銜接(因為凸點錫球融化后,變為液態,此時壓應力突然消失,貼片頭必須靠高精度的位置控制保持晶片和基板的距離);二是極快的加熱降溫能力,這是為了提高生產效率,如果以1分鐘加工1顆芯片的效率來估算,就算一條標準的TCB產線(包含4個熱壓鍵和頭) 12h加工能力不到3k顆,大概只有傳統的回流焊效率的十分之一到五分之一,這對量產來講簡直就是災難。
設備原型機的訂單很快拋給了幾家有實力也有意向的供應商,有的廠家看到技術指標大呼不可能,很快放棄了英特爾的橄欖枝。面對難以逾越的技術鴻溝,ASM Pacific一開始并不是最有希望的,但誘惑是巨大的,一旦成功ASM-P將晉升細分領域的頂尖玩家,執行業之牛耳。ASM-P為此做了充分準備,調動公司的一切資源,聘請行業的大咖,以期能實現技術上的突破,正如該公司一路走來發展為行業龍頭的故事的又一次重復。在此兩家深度捆綁,克服一個又一個的困難,最終實現了設備的成功開發,并于2014年將設備導入量產。對英特爾來講,全新理念的TCB設備讓該公司的封裝能力有了無限可能,除了更輕薄外,還可以做更復雜的封裝,比如EMIB,Foveros,3D Die Stack等等。而對于ASM-P來說,TCB的成功讓其一躍而成為封裝細分領域的龍頭之一,在先進分裝領域牢牢鎖定一席之地,此后ASM-P公司繼續在SMT行業攻城略地,續寫輝煌。
至此TCB修成了正果,下一篇文章我們將繼續探索英特爾公司在TCB上的各種工藝的開發和應用,以及其優缺點。
原文始發于微信公眾號(艾邦半導體網):熱壓鍵合(TCB)與英特爾的先進封裝
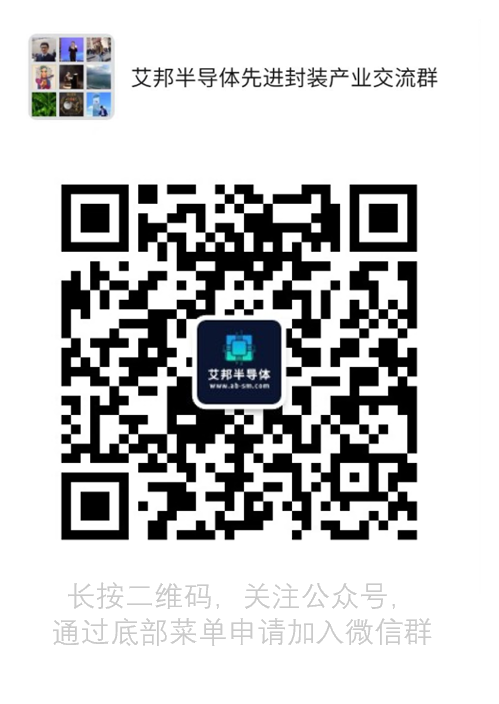